Trong nền kinh tế số và bối cảnh toàn cầu hóa, bài toán đặt ra cho các doanh nghiệp là làm sao kiểm soát tốt chi phí và cải thiện chất lượng sản phẩm, đồng thời đẩy nhanh quá trình phát triển và đưa sản phẩm ra thị trường. Điều này đòi hỏi công nghệ sản xuất mới đi kèm với sự phát triển của công nghệ số và áp dụng chúng vào quy trình sản xuất công nghiệp.
Công nghệ chế tạo dạng bồi đắp (Additive Manufacturing), còn được gọi là công nghệ in 3D, cùng với các công nghệ số được xem là công nghệ lõi của nền công nghiệp 4.0. Tuy nhiên, việc chế tạo bằng công nghệ in 3D không đơn giản là chuyển một mô hình thiết kế dạng 3D vào thiết bị sản xuất, ấn nút và chờ cho đến khi sản phẩm được chế tạo xong mà nó cần được thực hiện và kiểm soát chặt chẽ bởi một chuỗi các quy trình phức tạp và cần có sự hiểu biết nhất định để có thể tối ưu chất lượng sản phẩm đầu ra.
Bài viết này cung cấp đến người đọc một cái nhìn tổng quan và một số khái niệm cơ bản về công nghệ in 3D bao gồm: các định nghĩa cơ bản, điểm khác biệt của công nghệ này với các công nghệ chế tạo truyền thống, các ưu thế chính cũng như một số hạn chế của công nghệ in 3D, quy trình được dùng để chế tạo một sản phẩm hoàn chỉnh từ khâu thiết kế đến khâu hoàn thiện sản phẩm. Bài viết cũng sẽ giới thiệu một số phương pháp chế tạo chính trong công nghệ in 3D, đặc biệt cho vật liệu là kim loại và quá trình phát triển của các ứng dụng, tiềm năng của công nghệ in 3D trong sản xuất công nghiệp.
Công nghệ in 3D là gì?
Công nghệ in 3D (3D printing) hay Công nghệ chế tạo bồi đắp (AM: Additive manufacturing), được định nghĩa theo Hiệp hội Kiểm tra và Vật liệu Mỹ (ASTM: American Society for Testing and Materials) [1], là tập hợp các phương pháp gia công chế tạo trong đó sản phẩm được chế tạo bằng cách bồi đắp vật liệu theo từng lớp liên tiếp nhau từ một mô hình thiết kế 3D.
Công nghệ in 3D nói chung có thể được tóm tắt bằng một chu trình lặp lại hai bước liên tiếp dưới đây cho đến khi hoàn thành sản phẩm:
– Từ mô hình khối 3D, máy in sẽ tạo một lớp vật liệu với hình dáng hình học 2D được xác định theo từng lát cắt của khối 3D – lớp này được tạo thành từ các đường viền – và độ dày cố định trước. Nói một cách khác, từng lớp vật liệu chỉ được lắng đọng và liên kết lại với nhau ở những vị trí cần thiết theo mô hình thiết kế 3D ban đầu, nhằm tạo ra một lớp sản phẩm 2D.
– Tạo thêm một lớp 2D mới bằng cách bồi đắp thêm vật liệu lên trên lớp 2D đã được tạo ra ngay trước đó.
Như vậy, công nghệ chế tạo AM hoàn toàn khác biệt với các kỹ thuật chế tạo truyền thống như:
– Phương pháp gia công bằng cách bóc tách vật liệu (đẽo, gọt, chạm, khắc, phay, tiện, bào, khoan, v.v.) từ một khối mẫu thô ban đầu đến khi đạt hình dang mong muốn.
– Phương pháp tạo hình bằng khuôn như phương pháp đúc, rèn, dập nóng, v.v.
Ưu điểm và hạn chế của công nghệ AM
a. Ưu điểm
Công nghệ AM có nhiều ưu thế để trở thành một công nghệ có sức cạnh tranh với các công nghệ chế tạo truyền thống. Một trong số đó có thể kể đến khả năng chế tạo các sản phẩm phức tạp mà các phương pháp truyền thống khó hoặc không thể chế tạo được: sự phức tạp về cấu trúc, sự phức tạp về vật liệu và sự phức tạp về chức năng của sản phẩm.
Sự phức tạp về cấu trúc: công nghệ AM nhìn chung không bị giới hạn về cấu trúc hình học của sản phẩm cần chế tạo. Trong khi các phương pháp truyền thống giải quyết vấn đề hình dạng của vật thể cần chế tạo theo không gian ba chiều (3D) thì vấn đề này được chuyển thành một chuỗi các bài toán mặt hai chiều (2D) trong công nghệ AM. Đặc biệt, công nghệ AM có thể chế tạo các sản phẩm có cấu trúc dạng rỗng với hình dạng bất kì như kết cấu dạng giàn, tổ ong mà không cần phải dùng đến phương pháp bổ sung như cắt, gọt, khoan, đục, v.v. hoặc lắp ráp các chi tiết riêng biệt bằng phương pháp hàn, bắt vít, tán, v.v. Ngoài việc giảm chi phí về vật liệu, ưu điểm chính của những kết cấu này là cho phép chế tạo cấu trúc nhẹ để thay thế cho những cấu trúc dạng đặc truyền thống nhưng vẫn đảm bảo được các tính chất cần thiết trong điều kiện làm việc và khả năng chịu tác động cơ học tương đương, thậm chí vượt trội. Điều này cho phép giảm đáng kể số lượng quy trình và chi tiết cần chế tạo, từ đó giảm chi phí và thời gian sản xuất.
Hình 1 mô tả nút sáng (lighting node) của cấu trúc căng thẳng (tensegrity structure) tại The Hague được chế tạo bằng công nghệ truyền thống và công nghệ AM. Để chế tạo được nút sáng này, công nghệ truyền thống cần tạo ra 7 chi tiết khác nhau bằng phương pháp cắt gọt, sau đó nối chúng với ống trụ chính giữa bằng phương pháp hàn. Tuy nhiên, công nghệ AM, hay cụ thể hơn là phương pháp nung chảy giường bột (Powder Bed Fusion) cho phép chế tạo nút sáng nguyên khối chỉ bằng duy nhất một quy trình sản xuất và không cần dùng đến các kỹ thuật lắp ráp. Ngoài ra, quá trình thiết kế giúp tối ưu kết cấu bằng việc loại bỏ vật liệu ở những khu vực không cần thiết, cho phép giảm hơn một nửa khối lượng và tăng 45-75% độ sáng so với nút được chế tạo bằng phương pháp truyền thống [2].
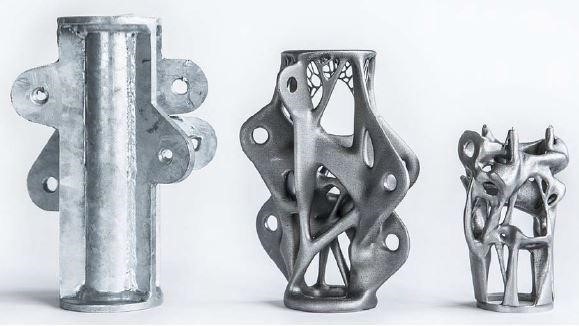
Sự phức tạp về vật liệu: trong một số trường hợp, sản phẩm cần được cấu thành từ nhiều loại vật liệu khác nhau theo bề dày nhằm phục vụ cho sự thay đổi chức năng theo vị trí trên sản phẩm. Trong một số sản phẩm, sự thay đổi vật liệu có thể diễn ra liên tục đồng nhất, còn được gọi là vật liệu chức năng (functionally graded materials) – (xem Hình 2.a) hoặc rời rạc bằng cách sắp xếp các lớp vật liệu riêng lẻ chồng lên nhau (xem Hình 2.b).
Trong trường hợp vật liệu thay đổi liên tục đồng nhất, thành phần hóa học và cấu trúc vi mô biến thiên đồng đều, từ đó tạo ra sự thay đổi liên tục về tính chất. Điều này giúp nâng cao khả năng làm việc và chất lượng của sản phẩm so với sản phẩm được cấu thành từ các lớp riêng biệt. Với công nghệ chế tạo AM, trong quá trình chế tạo theo từng lớp, vật liệu trên một lớp có thể được thay đổi đồng thời theo từng điểm, cho phép tạo ra những sản phẩm với tính chất riêng biệt. Hình 2.c và Hình 2.d giới thiệu chi tiết được chế tạo bằng công nghệ AM với thép 430 có từ tính và thép 316 không có từ tính nhằm tạo ra một sản phẩm có sự thay đổi về từ tính theo từng vị trí khác nhau, phục vụ việc hấp thụ chất gây ô nhiễm cho động cơ đẩy ion “Deep Space” của Cơ quan Hàng không và Vũ trụ Mỹ (National Aeronautics and Space Administration – NASA) [3].
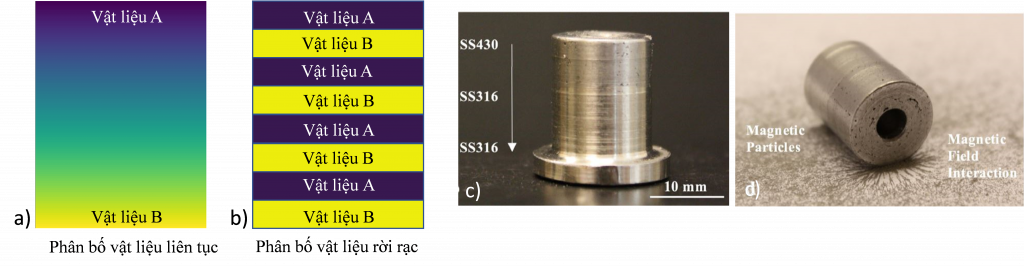
Sự phức tạp về chức năng: bên cạnh khả năng chế tạo sản phẩm có sự biến đổi liên tục về vật liệu nhằm tạo ra những tính chất riêng biệt, công nghệ chế tạo AM cũng cho phép thêm một số chi tiết bên ngoài vào sản phẩm trong quá trình sản xuất, tạo ra những sản phẩm với các chức năng phong phú hơn. Ví dụ, sản phẩm có thể được thiết kế thêm các lỗ trống với kích thước và hình dáng khác nhau chứa các chi tiết như đai ốc, sợi quang hoặc các bộ phận điện, điện tử và được đưa vào trong quá trình sản xuất. Việc này giúp giảm thiểu tối đa số lượng quy trình cần thiết để sản xuất một sản phẩm, hạn chế việc phải lắp ráp.
b. Hạn chế
Bên cạnh các ưu thế được kể trên, một số hạn chế chính của của công nghệ chế tạo AM có thể được tóm tắt như sau:
– Cho đến nay, các thông số từ thiết kế đến sản xuất của các phương pháp chế tạo trong công nghệ AM vẫn chưa hoàn toàn được kiểm soát, điều này gây ra khó khăn trong việc đồng nhất chất lượng sản phẩm được tạo ra, đặc biệt là cho các ứng dụng quan trọng trong lĩnh vực hàng không-vũ trụ hoặc quốc phòng [4]. Ngoài ra, một số tính chất như cơ tính của các sản phẩm kim loại được chế tạo bằng công nghệ AM (trước khi qua khâu xử lý sau sản xuất) còn nhiều hạn chế so với các sản phẩm chế tạo bằng phương pháp truyền thống.
– Sản phẩm được chế tạo bằng các phương pháp thuộc công nghệ AM thường có bề mặt không đồng nhất, gồ ghề và rất thô ráp, điều này ảnh hưởng nhiều đến mỹ quan và chất lượng của sản phẩm. Ngoài ra, tùy thuộc vào thông số sản xuất, sản phẩm tạo ra có thể chứa nhiều khuyết tật dưới dạng lỗ rỗng không mong muốn. Để giải quyết vấn đề này, nhiều biện pháp bên ngoài như tác động cơ học, mài mòn, phản ứng hóa học, xử lý nhiệt, áp suất cao, v.v. cần được sử dụng nhằm cải thiện chất lượng bề mặt cũng như làm giảm mật độ khuyết tật. Điều này làm tăng chi phí và thời gian, trong một số trường hợp còn gây ra khó khăn trong khâu xử lý do chưa thể kiểm soát được hết tất cả các thông số tác động của các biện pháp này lên chất lượng sản phẩm cuối cùng.
– Sản phẩm kim loại được chế tạo bằng công nghệ AM thường trải qua các quá trình nung kết hoặc thiêu kết ở nhiệt độ cao kèm theo đông đặc nhanh. Chu trình này được lặp đi lặp lại nhiều lần tạo ra sự biến thiên lớn về nhiệt độ, từ đó sinh ra cường độ ứng suất dư cao trong sản phẩm và có thể gây ra nứt, biến dạng hoặc gãy vỡ sau chế tạo (xem Hình 3).
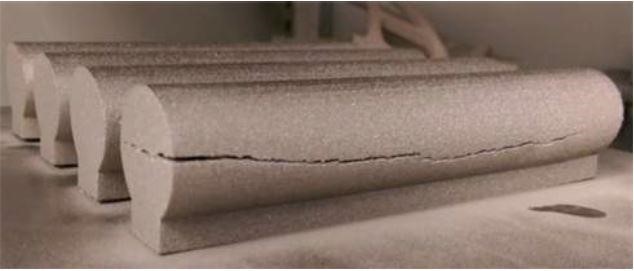
– Một số sản phẩm có cấu trúc phức tạp cần sử dụng bệ đỡ trong quá trình chế tạo, do đó cần được loại bỏ khỏi sản phẩm sau khi chế tạo. Tuy nhiên, việc loại bỏ những bệ đỡ này đôi khi gây ra nhiều vấn đề do vị trí đặt nằm ở những khu vực khó tháo dỡ. Trong một số trường hợp, bệ đỡ được kết dính chặt với sản phẩm và quá trình tháo dỡ bệ đỡ có thể gây ra hư hỏng, vết nứt không mong muốn cho sản phẩm [6].
– Kích thước của sản phẩm được chế tạo cũng có thể được xem là một hạn chế lớn đối với công nghệ AM. Hầu hết các sản phẩm được chế tạo bằng công nghệ AM thường có kích thước nhỏ. Mặc dù một số công ty có thể cung cấp thiết bị chế tạo với kích thước sản xuất lớn, tuy nhiên sự biến dạng của các bộ phận có kích thước lớn sau quá trình chế tạo vẫn còn là một vấn đề với công nghệ AM hiện nay.
– Không phải bất kì kim loại nào cũng phù hợp với công nghệ AM. Vật liệu đầu vào phải tồn tại dưới dạng lỏng, bột hoặc rắn (dạng sợi) tùy vào mục đích và phương pháp. Hiện nay, các nghiên cứu về nguồn vật liệu cho công nghệ AM ngày càng thu hút được sự chú ý, tuy nhiên số lượng kim loại và hợp kim phù hợp vẫn còn hạn chế. Đặc biệt, một số phương pháp yêu cầu vật liệu ở dạng đặc biệt như bột hay sợi với giá thành rất cao.
– Cuối cùng, kinh phí để đầu tư cho hệ thống máy móc và thiết bị cần thiết trong công nghệ AM vẫn tương đối lớn tính đến thời điểm hiện nay [7].
Các phương pháp chế tạo trong công nghệ AM cho kim loại
Hiện nay, công nghệ AM đã được sử dụng trên nhiều loại vật liệu khác nhau như polymer, ceramic, kim loại và hợp kim. Với sự cải tiến không ngừng, công nghệ AM liên tục phát triển với nhiều phương pháp chế tạo khác nhau nhằm đáp ứng nhu cầu ngày càng tăng trong sản xuất. Hình 4 giới thiệu các phương pháp chế tạo chính trong AM hiện nay.
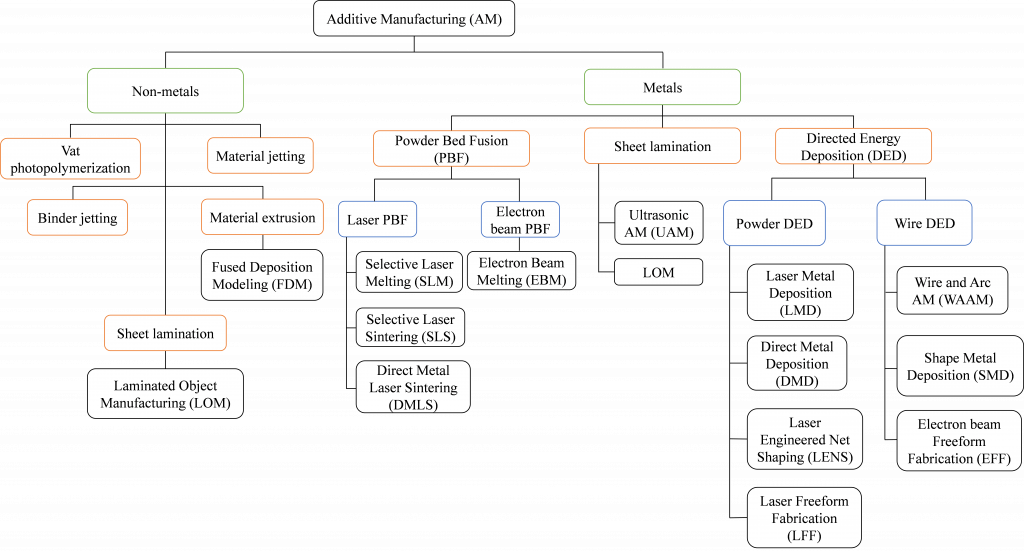
Sau đây, chúng ta sẽ tìm hiểu kỹ hơn hai công nghệ AM được sử dụng nhiều nhất cho kim loại là công nghệ nung kết giường bột (PBF: Powder Bed Fusion) và công nghệ lắng đọng năng lượng trực tiếp (DED: Directed Energy Deposition).
a. Công nghệ nung kết giường bột (PBF)
Trong công nghệ PBF, sản phẩm được chế tạo bằng cách sử dụng một nguồn năng lượng nhiệt lớn dưới dạng tia laser hoặc chùm electron để nung chảy một lớp mỏng bột kim loại được trải đều trên bề mặt chế tạo. Mỗi lớp vật liệu được nung chảy tương ứng với một lớp “ảo” được cắt ra từ dữ liệu thiết kế 3D CAD (Computer Aided Design). Trong công nghệ PBF, hai phương pháp chế tạo chính thường được sử dụng là nung chảy laser chọn lọc (SLM: Selective Laser Melting) và nung chảy chùm electron (EBM: Electron Beam Melting). Điểm khác biệt cơ bản của hai phương pháp này nằm ở nguồn năng lượng được sử dụng để nung chảy bột kim loại: SLM sử dụng nguồn năng lượng là tia laser và EBM sử dụng chùm electron. Vì lý do đó, phương pháp EBM được thực hiện trong môi trường chân không (áp suất thấp hơn 200 Pa so với áp suất khí quyển là 105 Pa) trong buồng sản xuất để bảo vệ nguồn electron. Ngược lại, phương pháp SLM có thể được thực hiện ở áp suất khí quyển. Tuy nhiên, trong thực tế, khi chế tạo bằng phương pháp SLM, một dòng khí trơ (ví dụ Ar: Argon) với áp suất cao hơn áp suất khí quyển sẽ được bơm vào buồng sản xuất với mục đích tránh phản ứng giữa sản phẩm được chế tạo ở nhiệt độ cao và oxy có trong không khí.
b. Công nghệ lắng đọng năng lượng trực tiếp (DED)
Trong công nghệ DED, sản phẩm được chế tạo bằng cách lắng đọng trực tiếp vật liệu xuống vị trí cần chế tạo mà không cần phải thực hiện quá trình dàn trải trước một lớp vật liệu như trong phương pháp PBF. Do đó, trái ngược với phương pháp PBF, trong phương pháp DED, bệ đỡ sản xuất thường không cần hoặc ít khi cần do các chi tiết của sản phẩm được định hướng một cách liên tục trong suốt quá trình chế tạo. Trong phương pháp DED, để chống lại sự oxy hóa, khí trơ sẽ được cung cấp một cách cục bộ trong suốt quá trình sản xuất bằng một ống phun khí đồng trục với đầu ra của vật liệu được làm nóng chảy. Hai phương pháp chính thường được sử dụng trong công nghệ DED là phương pháp lắng đọng kim loại bằng laser (LMD: Laser Metal Deposition) và phương pháp bồi đắp bằng hồ quang (WAAM: Wire and Arc Additive Manufacturing). Ngoài năng lượng được sử dụng, điểm khác biệt giữa hai phương pháp LMD và WAAM là nguyên liệu đầu vào. Phương pháp LMD sử dụng vật liệu dạng bột được nung chảy bằng tia laser, trong khi đó phương pháp WAAM sử dụng sợi kim loại được nung chảy bằng hồ quang điện.
c. So sánh giữa PBF và DED
Trong công nghiệp, công nghệ PBF có thể cho phép chế tạo sản phẩm với độ chính xác khoảng 0,05 mm, tốt hơn so với công nghệ DED với độ chính xác khoảng một vài mm [9]. Tuy nhiên, tốc độ chế tạo của các phương pháp DED có thể cao gấp 10 lần so với PBF [8]. Do đó, các phương pháp trong công nghệ PBF hợp cho việc chế tạo các bộ phận nhỏ có cấu trúc phức tạp còn các phương pháp thuộc DED thường được sử dụng để chế tạo các sản phẩm có kích thước lớn với độ chính xác vừa phải. Một trong những ưu điểm nổi bật của phương pháp LMD là nó có khả năng chế tạo các sản phẩm có sự thay đổi vật liệu liên tục (vật liệu chức năng như đã nói ở mục 2.1) bằng cách kết nối nhiều bình chứa bột khác nhau và điều chỉnh tốc độ phun của từng loại bột theo ý muốn trong suốt quá trình chế tạo.
Ngoài các phương pháp nung chảy vật liệu trên, một số phương pháp khác cũng thường được sử dụng để tạo hình kim loại mà không làm nóng chảy vật liệu đầu vào như phương pháp thiêu kết laser chọn lọc (SLS: Selective Laser Sintering) hay thiêu kết kim loại trực tiếp bằng laser (DMSL: Direct Metal Laser Sintering).
Quy trình chế tạo bằng công nghệ AM – từ mô hình đến sản phẩm
Như đã trình bày ở trên, công nghệ chế tạo AM cho phép làm ra một sản phẩm hoàn chỉnh từ mô hình thiết kế CAD 3D và đòi hỏi một quy trình bao gồm nhiều công đoạn khác nhau như được mô tả trong Hình 5. Toàn bộ quy trình chế tạo bằng công nghệ AM gồm 5 bước: xây dựng mô hình 3D; chuyển đổi và kiểm soát thông số dữ liệu; cắt lớp mô hình vật mẫu cần chế tạo; chế tạo sản phẩm; kiểm tra và xử lý sau chế tạo.
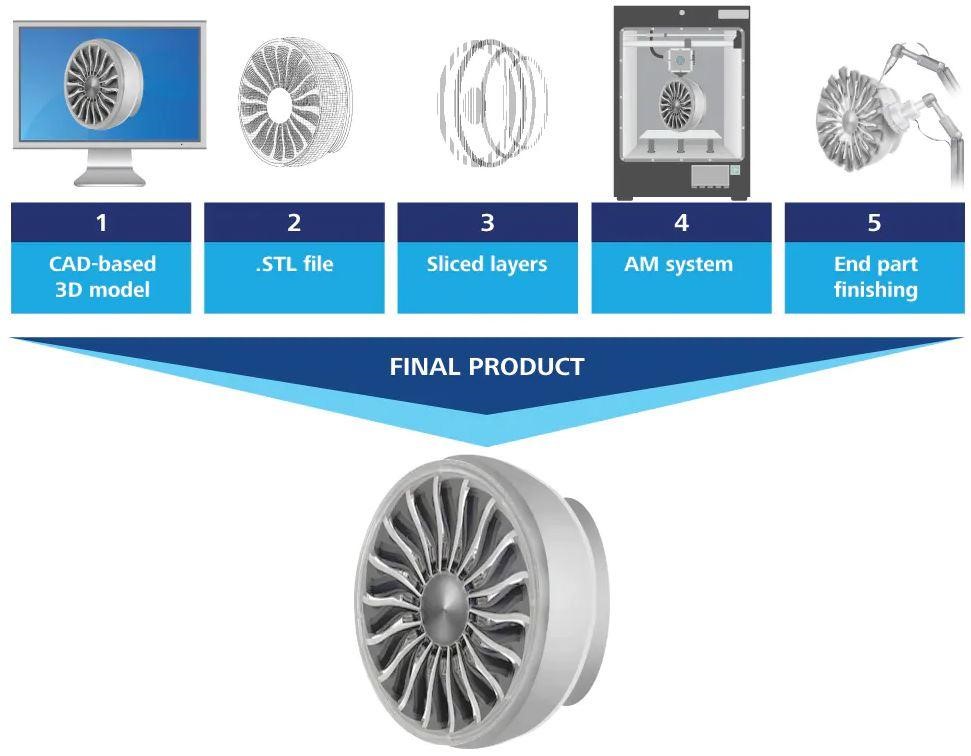
i. Đầu tiên, tất cả các chi tiết phải được thiết kế mô phỏng bằng một mô hình 3D nhằm thể hiện chính xác hình dạng hình học và cấu trúc mong muốn. Mô hình này có thể được thực hiện bằng nhiều phương pháp khác nhau, trong thực tế phổ biến nhất là sử dụng phần mềm CAD 3D hoặc thiết bị kỹ thuật đảo ngược (reverse engineering equipment).
ii. Sau khi hình dáng và cấu trúc của vật mẫu được thiết kế, phần mềm sẽ xuất ra mô hình dưới dạng một tệp .stl chứa tất cả dữ liệu thiết kế của vật mẫu. Dữ liệu sẽ được chuyển cho thiết bị máy sản xuất AM và các thông số sẽ được kiểm tra bằng phần mềm chuyên dụng nhằm xác nhận sự tương thích và các điều kiện phù hợp cho việc chế tạo.
iii. Tiếp theo, các tệp thiết kế CAD 3D sẽ được cắt thành các lớp 2D phụ thuộc vào độ dày của lớp vật liệu cần chế tạo và chất lượng của thiết bị sản xuất (các thông số này được xác định trước).
iv. Song song với quá trình cắt lớp, quy trình sản xuất được thiết lập bao gồm: định hướng và chu trình chế tạo (đây là thông số quan trọng vì tính chất của sản phẩm được chế tạo bằng công nghệ AM chịu ảnh hưởng nhiều bởi hướng chế tạo), vị trí của chi tiết cần chế tạo, bệ đỡ chế tạo, các điều kiện liên quan đến môi trường làm việc (áp suất, nhiệt độ, v.v.) cũng như liên quan đến nguồn năng lượng và tốc độ chế tạo. Sau khi các thông số này được thiết lập, việc sản xuất sẽ được thực hiện, chi tiết sẽ được chế tạo theo từng lớp cho đến khi hoàn thiện, hay nói cách khác là lớp cắt “ảo” cuối cùng được tái hiện lại trên chi tiết cần chế tạo.
v. Hoàn thiện sản phẩm: trên thực tế, việc xác định và chất lượng của bốn quy trình trước đó có ảnh hưởng lớn đến chất lượng của sản phẩm được chế tạo và từ đó ảnh hưởng đến số lượng cũng như loại phương pháp xử lý sau sản xuất cần thực hiện nhằm cải thiện chất lượng của sản phẩm. Có thể kể đến một số quy trình thường gặp như sau:
– Tháo dỡ bệ đỡ hỗ trợ sản xuất khỏi sản phẩm được chế tạo;
– Xử lý bề mặt bằng phương pháp cơ học hoặc tự động (điện hóa);
– Xử lý nhiệt nhằm làm giảm ứng suất dư trong các chi tiết kim loại. Việc này còn có tác dụng đồng nhất hóa cấu trúc vi mô và tính chất cơ học của sản phẩm;
– Tăng mật độ và giảm độ rỗng không mong muốn trong sản phẩm bằng phương pháp nén đẳng áp ở nhiệt độ cao (HIP: Hot Isostatic Pressing).
Sự phát triển của ứng dụng liên quan đến công nghệ AM
Được biết đến như sự bùng nổ về công nghệ kể từ khi bằng sáng chế đầu tiên của Hull [11] được công nhận vào năm 1986, công nghệ AM liên tục phát triển không ngừng cùng với tốc độ cải tiến nhanh chóng. Đến nay, ứng dụng của công nghệ AM có thể được chia thành ba nhóm chính bao gồm: tạo mẫu nhanh (rapid prototyping), sản xuất công cụ chế tạo nhanh (rapid tooling), và sản xuất trực tiếp nhanh (rapid direct manufacturing) [12].
a. Tạo mẫu nhanh
Công nghệ AM được sử dụng ban đầu với mục đích tạo nhanh mẫu thử nghiệm trong quá trình thiết kế và phát triển sản phẩm mới trước khi sản xuất đại trà [12]. Ứng dụng công nghệ AM giúp tiết kiệm thời gian từ lúc thiết kế đến khi đưa sản phẩm ra thị trường. Ngày nay, với sự tiến bộ về kỹ thuật và công nghệ số, ngoài các đặc tính thiết kế như kiểu dáng 3D, màu sắc, v.v., các tính chất của sản phẩm như khả năng chịu tác động cơ học, tính chất nhiệt, điện, v.v. có thể được kiểm tra và đánh giá một cách song song thông qua các mô hình vật lý. Đây là một công cụ hữu hiệu cung cấp cái nhìn tổng quan về sản phẩm trước khi đưa vào sản xuất; từ đó cho phép đưa ra những quyết định liên quan đến thiết kế và sản xuất ứng với đặc tính và tính chất của sản phẩm theo như mong muốn.
b. Sản xuất công cụ chế tạo nhanh
Công nghệ AM được sử dụng vào việc sản xuất khuôn với hình dáng phức tạp cho quá trình dập, ép, đúc, v.v. hay sản xuất các công cụ phục vụ cho các công nghệ chế tạo khác [12]. Đây có thể xem như là một ứng dụng gián tiếp của công nghệ AM vì nó được dùng để chế tạo công cụ sản xuất chứ chưa trực tiếp sản xuất ra sản phẩm. Việc ứng dụng công nghệ AM có thể giúp sửa đổi công cụ nhanh chóng mà không cần phải sử dụng các phương pháp truyền thống tốn kém và phức tạp như cắt, gọt, v.v. Hình 6 minh họa cho khuôn kim loại được chế tạo bằng phương pháp thiêu kết trực tiếp kim loại dùng để sản xuất bóng golf của nhà sản xuất EOS/Agie Charmilles.
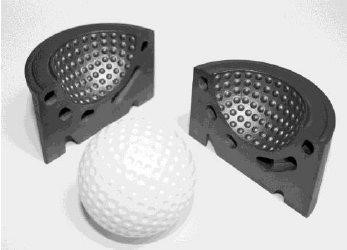
c. Sản xuất trực tiếp nhanh
Ứng dụng cuối cùng của công nghệ AM là sản xuất trực tiếp nhanh. Ứng dụng này nói đến việc sản phẩm cuối cùng trước khi được đưa vào sử dụng được chế tạo bằng một trong các phương pháp thuộc công nghệ AM. Cho đến nay, công nghệ AM không nhằm mục đích thay thế các công nghệ chế tạo truyền thống mà cung cấp giải pháp công nghệ mới nhằm giải quyết các giới hạn của các phương pháp truyền thống nhờ vào những ưu điểm nổi trội của nó.
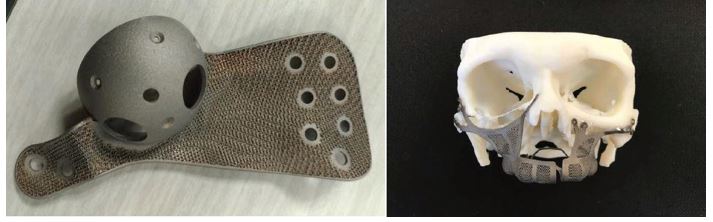
Hiện nay, ứng dụng của công nghệ AM trong công nghiệp chủ yếu tập trung ở một số lĩnh vực chính như: ô-tô, hàng không – vũ trụ, y tế và chiếm khoảng 50% tổng thị trường của ngành công nghiệp này (bao gồm gần 20% đến từ việc mua bán thiết bị máy sản xuất). Các ứng dụng thực tế của công nghệ AM chủ yếu được chia thành ba nhóm chính dưới đây:
i. Sản xuất theo yêu cầu: lĩnh vực sử dụng lâu đời và phổ biến nhất.
ii. Sản xuất với quy mô nhỏ các sản phẩm có giá trị cao: đặc biệt phù hợp cho ngành hàng không – vũ trụ và quốc phòng.
iii. Sản xuất theo mô hình “tùy chỉnh” liên quan đến các ứng dụng trong y tế như các sản phẩm được thiết kế đặc biệt dành cho từng khách hàng.
Tác giả: TS. Lê Hồng Thái, Dự án nghiên cứu “Tối ưu hóa quá trình chế tạo dựa trên dữ liệu từ mô phỏng vật lý – EDPOMP” VINIF.2020.DA15 (masda@tdm.edu.vn).
Biên tập: Quỹ đổi mới sáng tạo Vingroup (VinIF).
Tài liệu tham khảo
[1]. ASTM International, Standard terminology for additive manufacturing technologies: designation F2792-12a, ASTM International, West Conshohocken, PA, 2013.
[2]. S. Galjaard, S. Hofman, S. Ren, New Opportunities to Optimize Structural Designs in Metal by Using Additive Manufacturing, in: 2015: pp. 79–93. https://doi.org/10.1007/978-3-319-11418-7_6.
[3]. M. O’Brien, Existing standards as the framework to qualify additive manufacturing of metals, in: 2018 IEEE Aerospace Conference, 2018: pp. 1–10. https://doi.org/10.1109/AERO.2018.8396660.
[4]. Renishaw plc, Design for metal AM – a beginner’s guide: sacrificial supports additive manufacturing 3d printing metal laser melting residual stress, Https://Resources.Renishaw.Com/En/Details/Feature-Article-Design-for-Metal-Am-a-Beginners-Guide–111752. (2017). https://resources.renishaw.com/en/details/feature-article-design-for-metal-am-a-beginners-guide–111752 (accessed December 16, 2020).
[5]. B. Vayre, F. Vignat, F. Villeneuve, Identification on Some Design Key Parameters for Additive Manufacturing: Application on Electron Beam Melting, Procedia CIRP. 7 (2013) 264–269. https://doi.org/10.1016/j.procir.2013.05.045.
[6]. S. Mohd Yusuf, S. Cutler, N. Gao, Review: The Impact of Metal Additive Manufacturing on the Aerospace Industry, Metals. 9 (2019) 1286. https://doi.org/10.3390/met9121286.
[7]. C. Li, Z.Y. Liu, X.Y. Fang, Y.B. Guo, Residual Stress in Metal Additive Manufacturing, Procedia CIRP. 71 (2018) 348–353. https://doi.org/10.1016/j.procir.2018.05.039.
[8]. M. Cotteleer, J. Holdowsky, M. Mahto, J. Coykendall, 3D opportunity in aerospace and defense: Additive manufacturing takes flight | Deloitte Insights, Https://Www2.Deloitte.Com/Us/En/Insights/Focus/3d-Opportunity/Additive-Manufacturing-3d-Opportunity-in-Aerospace.Html. (n.d.). https://www2.deloitte.com/us/en/insights/focus/3d-opportunity/additive-manufacturing-3d-opportunity-in-aerospace.html (accessed December 16, 2020).
[9]. C.W. Hull, Apparatus for production of three-dimensional objects by stereolithography, US4575330A, 1986. https://patents.google.com/patent/US4575330A/en (accessed December 16, 2020).
[10]. A. Gebhardt, Understanding Additive Manufacturing: Rapid Prototyping • Rapid Tooling • Rapid Manufacturing, Carl Hanser Verlag GmbH & Co. KG, München, 2011. https://doi.org/10.3139/9783446431621.
[11]. R. Leal, F.M. Barreiros, L. Alves, F. Romeiro, J.C. Vasco, M. Santos, C. Marto, Additive manufacturing tooling for the automotive industry, Int J Adv Manuf Technol. 92 (2017) 1671–1676. https://doi.org/10.1007/s00170-017-0239-8.
[12]. N.-D. Ciobota, G. Gheorghe, V. Despa, Additive Manufacturing as an Important Industry Player for the Next Decades, Scientific Bulletin of Valahia University – Materials and Mechanics. 17 (2019) 68–71. https://doi.org/10.2478/bsmm-2019-0010.